Assembling the Leader Evaporator Half Pint - Parts 3 and 4 of 4
Moving of the bricked arch to the sugar house, leveling the arch/evaporator, installing the stack, and the first (test) boil using water and baking soda
In this installment will be documented the moving of the bricked arch to the sugar house, leveling the arch/evaporator, installing the stack, and the first (test) boil using water and baking soda.
To see how we got to this point, see:
Part 1, "Assembling the Leader Evaporator Half Pint - Part 1 of 4,"P
Part 2, "Assembling the Leader Evaporator Half Pint - Part 2 of 4,"
We knew that moving the arch from the house to the sugar house would be "challenging." Unfortunately the controlled environment of the house was necessary to facilitate the curing of the refractory cement used in the process of installing the firebrick. Getting the sheet metal and cast iron shell of the arch into the house was no real problem, Geri and I accomplished that in less than 30 minutes, using only the garden cart as a simple machine.
Moving the firebricked arch out to the sugar house, and getting it up onto its foundation, was another matter altogether. The firebrick alone weighs ~200 lbs, plus at least 3 gallons of refractory cement (MEECO'S RED DEVIL 610 Refractory Cement ), that is ~60 lbs, plus the weight of the arch shell, I put that at 50-75 lbs, and we are somewhere between 310 and 325 lbs of dead weight. We used a few 2x4's that were lying around, and fashioned a sort of litter, although carrying the arch in that way simply did not work for more than a couple of steps. We ended up sliding the 2x4's under the arch, picking up one end, sliding the arch down to the other end, and repeating that process, a couple steps at a time. It literally took four men to lift and carry the arch out of the house, with an additional man to supervise the operation. Things got a bit easier after the arch was clear of the house.
Once outside the house, we manhandled the arch onto the utility trailer, and towed that behind the UTV over to the sugar house. Then, more brute force getting the arch off of the trailer, into the sugar house, and onto the pads I had prepared for it. Moving the arch from the house to its pads in the sugar house, was definitely to toughest part of the commissioning job.
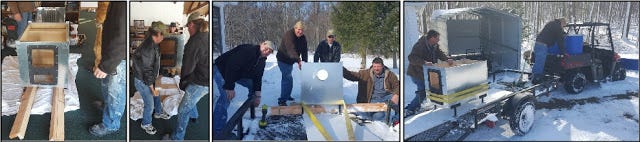
After the arch was on the pads, we leveled it front to back, and side to side, using a 4 foot level and softwood shims of the type that are normally used to level and plumb a door or window frame.
The final step of the arch installation, was to install the stack. Dennis and Nathan had helped me to select the various straight sections, elbows, and the cap we would need, all in 6 inch diameter stove pipe from the local hardware store. At first I had thought that we would go straight up through the roof, but as usual, two or more heads are better than one, and we decided to go up and out the back of the sugar house, between the top of the rear wall and the peak of the roof. The amount of vertical stack recommended by Leader Evaporator is a minimum of 9 feet; when assembled our stack stood with a height from arch outlet to stack cap at 7 feet.
The assembly and installation of the arch having been completed, the next step was to put the Boiling and Reservoir Pans on the arch, and then to conduct the test boil.
As it turns out, we actually performed two test boils. During the first, we just could not seem to get the entire boiling pan to a rolling boil. The solution to this problem brought to light that it is not enough to simply Read The !@#$%^& Manual, one must also adhere to the manual, or understand completely why it is unnecessary in a particular case. The fact that enough vertical stack height had not been installed, proved to be the problem.
Perhaps counter-intuitively, the draft (flow of combustion air) into the fire box and up the stack, is directly proportional to the height of the stack. Another whodathunkit moment! I do not know how often I have proven my high school math teacher, Mr. Lauer, correct; all of those equations, and more importantly the science behind them, do come in handy. Teenagers can be such asses, and I was no exception! I suppose I am still no exception from time to time.
Per that go-to source, Wikipedia, Flue Gas Stack (https://en.wikipedia.org/wiki/Flue-gas_stack):
Flue-gas flow-rate induced by the draft[edit]
As a "first guess" approximation, the following equation can be used to estimate the flue-gas flow-rate induced by the draft of a flue-gas stack. The equation assumes that the molar mass of the flue gas and the outside air are equal and that the frictional resistance and heat losses are negligible:.[5]
where: Q = flue-gas flow-rate, m³/s A = cross-sectional area of chimney, m² (assuming it has a constant cross-section) C = discharge coefficient (usually taken to be 0.65–0.70) g = gravitational acceleration at sea level, 9.807 m/s² H = height of chimney, m Ti = absolute average temperature of the flue gas in the stack, K To = absolute outside air temperature, K
____________________________________
What does all that mean? Well to me it means that the flow rate of combustion air through the arch and up the stack is proportional to the square root of the the height (H) of the stack. So, if we assume nothing else changes, and we increase the height of the stack from "1" to "1.3," or a 30% increase, the change in the flow rate would be increased by √1.3 - √1 = 1.14 - 1 = 0.14 or 14%. In other words, if the stack is 10 feet, and I increase its height to 13 feet, the flow rate through the arch will be increased by 14%, which means hotter fire and more sap evaporation.
I trust someone will check my my math and comment if it is incorrect.
Based on that analysis, we added 3 feet to the 7 foot stack, and voilá, blast furnace-like performance of the arch and evaporation rates within Leader's specified range. Heck, I may try adding another 3 feet for 2017.
According to Leader Evaporator: The first boil is done to remove any residual materials from the pans and to “season” the bricking and insulation. 1. Prepare 15 gallons of a baking soda and water mix in proportion as follows: a. 1-1/4 ounce of baking soda b. 15 gallons of water 2. Fill the boiling pan with the baking soda : water mix to a level of approximately 3 inches. 3. To season the bricking, start by building a small fire in the fire box and very gradually build to a normal fire. 4. Boil the solution for approximately 30 minutes. Watch the boil carefully and replenish the solution as needed to ensure the solution in the pan remains at approximately the 3 inch level. 5. Check all equipment: a. No leaks at fittings b. Pan is boiling evenly c. Valves work properly d. Draft is correct (pan boils evenly) 6. Drain the baking soda solution from the pan. Rinse the boiling and reservoir pans thoroughly with clean unsoftened, non chlorinated well or spring water. Drain the water and dry the pans.
Having finally satisfied element 5 d., we were able to drain, rinse, drain again, and dry the Boiling and Reservoir Pans, making us ready for evaporation of the first sap of the season.
-- John, 25 Apr 2016
Earn rewards by referring a friend!