The Quarter-Sawing Process, and Problems, Oh No!
Quarter-sawing is simple I suppose, but tedious work, and requires about twice as much time as plain sawing
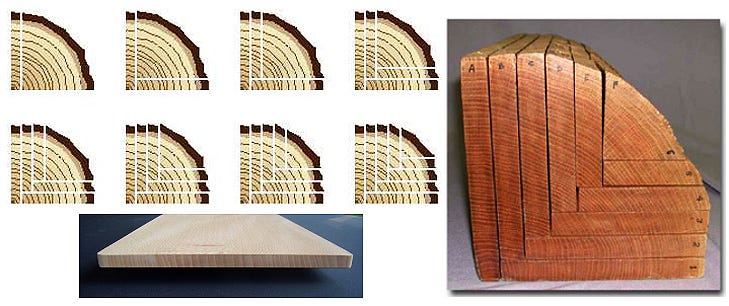
The first step towards improving any process, is to understand the current state of the process, and in my opinion formally documenting that process in words and pictures is a solid foundation for improvement efforts. It's important to keep in mind that this process is not the "be all and end all" just because it is documented; it is though the process currently in use.
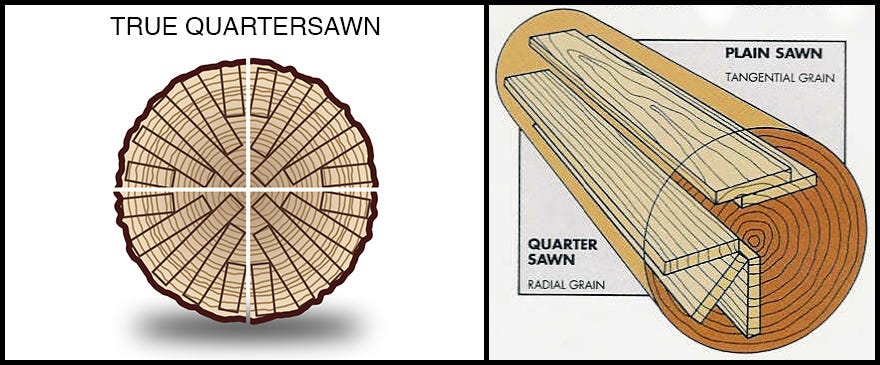
There are several methods for approaching "true quartersawn" lumber using a band-sawmill like the Wood-Mizer, and it is likely that we have experimented or will experiment with most of them. For high-value lumber, the most important metric, at least from our current point of view, is the amount of quartersawn lumber yielded from a given amount of quartersawn lumber in the log in the ideal case. So far, it has been our experience that the in-use process, as compared to "plain sawing," is less efficient terms of board feet/hour produced, by a large margin. The primary reason for this is the amount of log and cant handling required; first halving the log lengthwise, pushing one half off of the mill, cutting the remaining half into quarters, pushing one of the quarters off of the mill, processing a quarter, retrieving the quarter already cut for further processing, then the half already cut, and so on. The process runs on like the sentence before this one. Time-wise our experience has shown that it takes at least twice as long to make quartersawn lumber as compared to plainsawn, all else equal; that is true whether we talk about board feet per clock hour, board feet per machine hour, or board feet per labor hour.
The process selected for quarter-sawing on the mill, also depends on processes post-milling. For example, in the context of making what I am calling "stave blanks," we will provide a "stave board;" our customer will then cut the stave blanks from the stave boards. Normally at the mill, the board would be edged on both sides, resulting in a board of uniform width from one end to the other. However, trees are not perfect cylinders, and while the International 1/4 Inch Log Scale assumes taper of just 1/2 inch in diameter for every 4 feet of log length, the taper can be much greater in the butt log (the first log above the ground), a log valued for its clarity, i.e. the absence of knots. In the veneer business, flooring, and staves, the value of the butt log can be 50% or more greater than the value of the second log, per board foot. With a 10 foot butt log, if we retain the full width of the quartersawn board, the customer can first crosscut that board to length, let's say 36 inches, and then rip each of the three resulting boards to maximum width, with the board nearest the butt potentially an inch or more greater in width than the other two boards. Therefore, we leave a "live edge" on each board. As we progress other factors, like clarity or grade of lumber produced, may prove to be as or more dominant, changing our perspective on which of the various base processes might be best in the situation.
Here then, in words and pictures, and in reference to the above process flow diagram, is more detail regarding each step of the current process:
Set-up Mill. Side supports up, log loader, clamp and lo turner down.
Position Log on Log Loader
Load Log
Position Log Axis in a X-Y Plane || Mill Deck. || means "parallel to." The X-Axis runs the length of the mill, the Y-Axis runs across the mill, and the Z-Axis is the vertical. X-Y planes are || the deck of the mill.
Halve the Log in X-Y Plane
Remove Top Half to Log Loader
Halve the Bottom Half
Remove Top Quarter to Log Loader
Clamp the Cant (bottom quarter)
Cut Board from the Cant Bottom
Move Clamp and Cant Outboard
Remove Board to Drying Stack (no image)
Quartersawn Board in Cant?
Yes
No
Rotate Cant 90° Around X-Axis
Remove Cant for Secondary Use (no image)
Cant on Log Loader?
Yes, 1/4
Yes, 1/2
No
Retrieve Cant (1/4) from Log Loader
Retrieve and Clamp Cant (1/2) from Log Loader
Halve the Cant
Remove Top Quarter to Log Loader
Log in Pile?
No (no image)
Yes (no image)
Whew! That's a lot of log handling, hence the high cost of quartersawn lumber. It is our goal to continuously improve our efficiency in producing quartersawn lumber, and to improve the quality of that lumber. As a first step, let's say that we want to double our efficiency, and from that vantage point we think of everything preventing us from achieving that objective as a problem. Below then are the first "problems" identified with our current process:
Problem: Making sure the small end of the log, and preferably both ends, span one or both of the mill toe boards; if the small end does not span a toe board it cannot be raised to put the axis in a X-Y plane
Problem: Small end of the log is at the rear of the mill; makes centering the axis more time-consuming
Problem: Positioning the log axis in an X-Y plane above and parallel to the mill deck quickly and accurately, using log turner, clamp, and toe boards
Problem: When cutting up from the deck at the 1" mark, returning to that mark every time is by eye and manipulation of the carriage height; time consuming and imprecise
Problem: Moving the cant to outboard (for board removal) with every cut on a quarter
Problem: Moving half of the log on the log loader, and then back onto the mill
Problem: Having to quarter half the log, instead of being able to quarter the whole log before removing 3 quarters from the mill to work on the first 1 quarter
Problem: Setting the clamp for just less than 1 inch above deck height, repeatably and quickly
Problem: Deciding whether to turn the cant, or not, to achieve growth ring angles within 60 to 90° of the board surface
Problem: Cutting up from the mill deck through the quarters means the remaining portion of the quarter needs to be removed to get the board off of the mill
Problem: Side support, specifically the 4 individual points against which the log is forced by the clamp when cutting 1 inch off the deck (the movable side supports are lowered completely in this situation); the log will sometimes ride up and over the supports, or the shape of the log edge is such that contact is made with only 1 or 2 of the supports, or the edge of the log is soft
Problem: Stresses in the log cause it to "bow;" it does not lay flat on the deck, resulting board is thin at one or both ends, especially the first board cut from a quarter
Problem: Stack for air drying cannot be lifted as-is by forks onto transport to customer; unnecessary log/lumber handling
Problem: Transporting stickered stack of lumber may result in looser stack, potentially unsafe, an inefficient use of vertical space
Problem: Butt end of log too big to pass through throat of mill
Problem: Flare, the difference in diameter between the small and large ends of the log, is too great to allow centering with available travel of the toe boards
Problem: Knots, especially near the center of the log
That we have "problems," does not mean anything is "wrong," per se. It does imply that there might be opportunities to improve, in some instances substantially. There is nothing glamorous about going to work every day and chipping away at problems, but, I am convinced that that is how the good become great, and perhaps even more importantly, stay great.
All the best, John
John:
Paul File here:
269-208-1260
Give me a call we need to cut some 15” 15in x15in ….” 6-8-10 ft solid wood bench’s for the Marion- Mag. Wedding venue seating.
Need to schedule @ your earliest convenience.
Thank you.